Organisations have sometimes been surprised and disappointed when they re-engineer a forms-based data capture process but fail to achieve their anticipated savings. This paper, presented to CIMTECH 1999 and 2000, explains:
- how capture costs are built up from data entry plus dealing with problems;
- an example of costs for an automated process and for dealing with the paper forms that are left after you bring in an internet process;
- four techniques for investigating the costs of your current process.
Overall, you will be able to understand your own process and find out whether automation will achieve what you expect from it.
The costs of data capture are the overall cost of turning documents into data
The costs of data capture are the overall costs of turning incoming documents into data used in a business process. I’m assuming that mostly, the documents are forms and you want to process those forms within your organisation.
If you are considering automated data capture in your organisation, you may have seen schematics like this:
Documents arrive at a scanner, are captured, and end up on your organisation’s database.
The problem with these schematics is that they leave out one major element of your costs: the staff who operate the technology. I will not be considering the technology in this paper. Instead, I will be considering the human element: what your staff have to do at each stage to achieve the overall business purpose.
Here is another schematic of capture:
This paper will describe:
The costs: what people have to do at each stage when turning paper into data.
How the numbers work: an example of costs for an automated and for an internet process.
Investigating your costs: four techniques for investigating the costs of your current process.
Someone must open and sort the post
Your documents do not arrive at the capture process by themselves. Someone has to open and sort the incoming post, or to identify the document that will be captured in some other way.
When you start scanning your documents, rather than reading them, you have to be more careful when you open the post.
For example, one of my customers complained that “the scanner does not work”. I found that they were opening the envelopes with an automatic letter opener which sliced each form into two pieces. Then the data capture department was sticking the pieces back together with sticky tape which was too thick for the scanner.
Your incoming post probably includes some of these:
- incoming cheques and other forms of money
- items marked ‘personal and confidential’
- post for a different office
and various other items which may or may not have an impact on the process you are automating. Somewhere you will need to have a post sorting station like this:
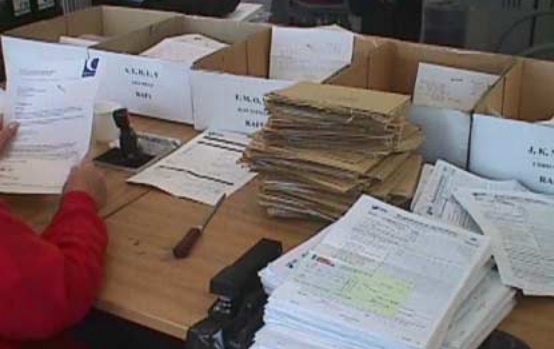
Your post team will need to know what to do with all your forms. Are you going to get them to remove the forms that are too torn or crumpled to go into the scanner? What about forms which arrive on the old version of the stationery? What are you going to do if an incoming form is attached to a letter? Are you going to deal with it as a letter or a form first? What if the letter modifies the contents of the form?
Marks on paper need to turn into useful data
Once you have got your forms to your data capture staff, the next step is turning paper into data.
In a conventional data capture process, a member of your data capture staff:
- reads each form and decides what to type in (recognise fields to type)
- types the letters or number into the appropriate field on the computer (type in data)
- deals with any validation that the computer throws at them (repair).
Repair is the process of dealing with the validation failures and any other problems on the form, and is typically the most time-consuming and error-prone part of the process.
Recognition is not straightforward
Here is a typical box with a number written in it. The process of recognition is understanding the squiggle in the box as a number. Humans are rather good at this, and most of us will interpret these squiggles as the number ‘3’. You might not even notice that the ‘3’ has been written across part of its box.
Here is same box as a bitmap (only half the bitmap is shown):
To recognise this as a number, the computer has to hunt for the dots that will create a number. When character recognition experts – optical character recognition (OCR), intelligent character recognition (ICR), neural network recognition (often called Artificial Intelligence or AI), or whatever – talk about recognition, this is what they mean. Their equipment will look for the squiggles, separate them from the boxes, and turn them into numbers. They prefer to have the boxes printed in dropout colours so that they do not need to deal with problems like my ‘3’ touching the box it is in, but some recognition engines will sort this out for you.
When character recognition vendors talk about 90% recognition rates, they usually mean that 90% of characters written in the boxes will be recognised correctly.
Extra marks cause difficulties
Unfortunately, customers do not always write clearly and neatly in the boxes.
This time, we have another ’31’ but the customer has felt obliged to indicate ‘zero’ with two horizontal slashes. Some OCR engines may fix this. Mostly, your engine will report this as a recognition failure.
Validation failures are common
Your computer system is likely to have validation on the input. For example, the amount field might only accept numbers in the range 0-9,999,999 and the validation will reject all of these:
Your staff will sort these out when they see them.
It is likely that a recognition engine, with appropriate definitions and validation, will also refer them to the operator although there is a risk that the third of my examples would be captured as 1,257,816 rather than 12,578,163.
Mixed mode problems happen often
In this case, the customer has added a decimal point and two zeros. What happens here depends on the validations and the engine. You may have a recognition failure on the decimal point. If you are in luck, you will get ‘31.00’ back from the engine and you can then strip off the ‘.00’ to put 31 into your database. If your engine and validations are not working in harmony, you may end up with ‘31100’ in your database.
Multiple entries and messages also happen frequently
Quite often your customer will do something like this:
Whatever did they mean?
A good OCR engine will give up on these – and is unlikely to count them as part of the 10% recognition failure. If the OCR tries too hard to understand the writing, you may get strange results: ‘300211’.
Repair is the process of dealing with failures
‘Repair’ is dealing with recognition and validation failures. A person has to view each one, and decide what to do at one of these levels:
- Visual: You can repair the problem just by looking at the field. The ‘extra marks’ example is a visual repair.
- Validation: You may need to know the validations as well, as in most of the ‘validations’ examples.
- Internal fix: You can solve the problem with information on the document or within your organisation.
- Go back: You have to obtain more information from your customer to solve these problems.
Let us look a bit more closely at the ‘internal fix’ and ‘go back’ levels.
Internal fix means using other data you hold to help with repair
I have concentrated on a numeric field, but frequently your customer will forget to supply some information you need: their account number, postcode, or previous order reference number. Quite often, you can look these up in your existing records.
You may need to know some business rules to fix some validation errors. For example, your staff will probably know if you can deal with an amount of 12,578,163 – or whether the customer really meant something else, maybe £125,781.63.
Go back means asking the customer
Organisations are reluctant to send forms back to the customer, but you may have to – for example, if a signature is missing, you have to ask the customer what was meant, or for extra information to solve a problem.
If the customer has given both addresses on the form, then this could be an ‘internal fix’. If not, we have a ‘go back’ example.
People usually combine repair and data entry into one process
The diagram shows three separate processes of recognise, type in and repair. In fact, your staff will look ahead and choose a repair strategy before typing anything. They will read the marginal comments and deal with them first. And they will also know a lot of the validation rules. A human is unlikely to type ‘31100’ in my ‘wrong format’ example. ‘THIRTY’ would be translated to ’30’. A human would probably never realise that they have seen an ‘extra marks’ problem.
Repair is more complex in an automatic data entry process
When you use an automatic data entry process, there is much less flexibility in the process. Recognition always comes first: the engine has to try to reconcile the squiggles into letters and numbers. You can only proceed to the validation stage when you have actual data. The ‘internal fix’ and ‘go back’ problems, which should have been tackled before you tried to do anything with the form, may get left until the end or missed altogether.
Repair changes when you move to an internet form
If you put your form out to your customer on the internet, then you will solve some of these problems.
The visual problems, such as extra marks, go away. Your form will only accept data that is appropriate for the box.
Validation errors will be fewer. Many validations can be done immediately, so that the customer corrects the problem for you.
However, “internal fix” problems that you could sort out from data you hold are a worse problem on the internet. Your customer is unlikely to have access to the same information.
Finally, “go back” problems where you have to approach your customer for more information are also likely to be worse. It may be that your form asks for a mandatory field that your customer cannot understand, or (for some reason) refuses to supply at first. If your internet form rejects incomplete data, you may never find out that your customer attempted to fill in your form. If you are unlucky, that might be a customer who goes away.
Both data and paper have roles later in the process
Once you have taken the data from the paper, your final step is to make use of the information.
A paper form is often more than the data written on it
Even though you have lifted the data from the paper, the paper itself often has its own roles:
- As an instruction to later parts of the process. For example, you might use the order form as a pick list to create and pack the order.
- As a record of who did the work. For example, your staff may sign or mark the form to take responsibility for processing it.
- To control workloads. For example, your supervisors may judge the amount of overtime they need based on the height of the pile of unprocessed forms.
If you decide to remove paper from your process, you will need to find out all the things you use the paper for so that you can develop an alternative method.
Find out whether the data you expect to capture is useful
The final question to ask is: what are you actually capturing at the moment? When you bring in your automated process, you may find that costs go up because you start to capture data that you did not capture in the manual process.
This may seem strange. If you have a box on the form, and the customer has completed the box, why would you ignore it?
You may be asking customer to tell you things that you already know
Consider this example:
The customer here has filled in his name (and goes on to fill in his address) even though the name and address are the same as the ones already printed at the top of the form. There is no need to capture anything. ‘Change’ of name and address boxes are notorious for this: in one study, I found that half of the entries in the change of address box were the same as the current address. Often, the form asks the customer to fill in the whole name and address even if only one part of it has changed: you may be processing 50 to 100 characters of information when the only change is a single digit in the postcode.
I have chosen name and address because so many forms ask for them. But the problem of asking for information you already hold is much more pervasive than just name and address. On the form I used for the example above, every entry was the same as the previous year’s data.
Information may arrive more than once
The second hidden cost I want to remind you about is the cost of getting the same information from two sources. For example, some of your customers may place orders twice: once by telephone or internet, and then a second time on an official order form. Although you may try to discourage them from doing this, you do not really want to put them off placing an order with you. So how are you going to reconcile two versions of the same data?
All boxes on the form are not equal
I have been discussing forms as a whole. But when you consider the individual boxes, you may find that:
- Some are crucial to your business: perhaps the signature box, or the credit card number. We will assume that you capture these.
- Others are for more general purposes: market research, future mailing lists, a description which helps to confirm the product reference number. Your manual process might only capture these for some forms, or for certain special events, or if other information is missing.
- Some may just be left over from an earlier version of the business process and are no longer used at all. If you simply start to capture all the boxes on the form when you introduce your automated process, you may be using a lot of staff time on recognition and repair for boxes you are not going to use.
It is important to distinguish between these boxes when you design your automated process. A validation which accepts almost anything on a vague box about ‘please indicate your leisure interests’ might be inappropriate for a box, similar layout, asking ‘please indicate your choice of product colour’. If a box is only used under certain circumstances, it might be more efficient to ignore recognition errors on it until the point it is needed.
Rework happens when something goes wrong
So that leads me on to my final category of problem: rework. If you miss problems at the initial capture stage – whether because your staff got it wrong, or your automated process got it wrong – then you have to solve the problem later.
People make mistakes all the time. You may find out that the capture process has gone wrong when you deal with the information. Or possibly your customer will point out the mistake and allow you to put it right.
To simplify the calculations, I have grouped all of these into one overall category: rework.
A full capture schematic starts and ends with the customer
Each stage in the process has a cost
A typical mixture of costs includes easy, ordinary, and problem examples
Let us now look at how repairs influence costs for dealing with forms. There will be a range of difficulty, but I will simplify them into two types:
Easy – The simplest forms – less data and no complications. Time to process = about half the time of an ‘ordinary’ form = .5 unit
Ordinary – The run-of-the-mill work. ‘Typical’ forms with an average amount of repair. Time to process = 1 unit.
We also identified three types of problem forms:
- Internal fix – Repair from information you already hold. Same basic time as an ordinary form, plus about the same again to deal with the problems. On average, these take about twice as long as an ‘ordinary’ one = 2 units.
- Go back – Need to go back to the customer during initial processing. Same basic time as ‘ordinary’ plus time to contact customer, retrieve information, and finish. A working assumption: 4 times as long as an ordinary form = 4 units.
- Rework – Someone points out a problem later. Has to be re-worked plus there will be additional care and attention needed. Some of these will take a long time to sort out, but to keep the calculations simple we will assume 2 units more than a ‘go back’. Total time = 6 units.
The mix of work will vary according to the application, but the table below shows a typical split and the effect on process time. For each type, I have worked out:
- typical percentages in the overall mixture
- the time for processing the form
- split overall time into post handling, keying, and problem handling.
An automated process also has costs
Let us now consider the effects on these times of an automated capture process. You will replace your keying time with automatic recognition.
As you are now scanning your forms, you have:
- post handling time – doubles – now 6% of unit time
- scanning time (new) – typically 10% of the previous unit time
The original keying time is replaced by:
- recognition failures – 10% of the data will need repair because of not being recognised – 10% of previous keying time for the form.
However, from the earlier discussion of errors you will recall that there are other reasons for repair. The automated data capture product will not deal with ‘extra marks’ or ‘wrong format’ errors. So we need to add:
- validation failures – maybe 10% of previous keying time
- extra marks – maybe 10% forms will have this problem throughout, but to keep it simple we will use 10% of previous keying time per form.
On top of that, we will actually increase the time for dealing with our problem categories of documents. With the manual process, we could recognise the problems and start to deal with them immediately. With an automated process, these problems get left until the recognition and validation problems have been identified. This increases the time to deal with each problem: the ‘problem penalty’.
There is also a probability that problems get missed during the data capture stage, as some forms will no longer be getting the same scrutiny as they used to. Therefore some work has to be put right at the later stage. The effect is spread among all the forms, but to keep the calculations simple I have just assumed that ‘ordinary’ forms are affected.
The overall effects will depend on your particular process, but as a first estimate let us assume:
- time to deal with problems increases by 30% (problem penalty)
- 3% of forms move from the ‘ordinary’ into the ‘rework’ category.
Automated capture reduces some costs and increases others
The chart compares the manual process with the automated process.
This is rather a successful implementation of an automated data capture process. The new process is a bit more problematic for the difficult forms, and there are a few more of them. But 85% of our forms are being dealt with more quickly.
The table below puts this into numbers:
The bottom line is that the time saved on dealing with the easy and ordinary forms is offset by the increased time on the problem forms. Our new technology has achieved (161-154) / 161 = 4% saving.
An internet process changes the costs again
So how about considering an internet process instead? Let’s assume that you offer both an internet form and a paper form to your customers. For the moment, we will ignore the cost of providing the internet option, and look only at the impact on the cost of staff who deal with the paper forms.
It is likely that the customers who opt for internet are those who are coping well with your paper form. We will be optimistic and assume that 80% of your ‘easy’ forms now arrive by internet, and 60% of your ‘ordinary’ forms.
- “easy” forms – 20% of previous levels
- “ordinary” forms – 40% of previous levels.
Against this, we have:
- double filing – some customers will send in paper and internet – perhaps 10% of your internet customers
- problem penalty – with a more complex process, there are more things to go wrong. Some problems will take longer to sort out. As with the automated capture process, I have assumed that problems take 30% longer to solve.
- forms change category – some forms will move from the ‘ordinary’ to the ‘rework’ category. As with the automated capture process, I have assumed that 3% of forms change category.
We will also ignore any additional costs for helping your customer to solve problems with the internet forms. We will assume that they don’t give up on your organisation, but instead persist is sending in the ‘internal fix’ and other problem categories of forms in the same numbers as before.
The new mixture of forms is shown on the next page.
Even allowing for the people who are sending their forms in twice, we are now handling only 61.3% of the forms on paper that we processed before we introduced the internet option.
In the old paper process, it took us 161 units of time to deal with 100% of the forms:
Dealing with paper forms after introducing the internet option:
Putting the two tables side by side shows that the new process has not achieved the savings that we expected.
The total cost is now 154.7 which means: (161-154.7)/161 = 4% saving.
Offering an internet option creates a “richer mixture” in your paper forms
In many organisations, the less experienced staff deal with the easier forms and the more experienced tackle the problem forms. If you add an internet option without tackling your problem forms, you’ll find that the easy ones now mostly arrive by internet, and the remaining paper forms – while fewer overall – now have a higher proportion of forms with problems on them. You’ll need fewer of the cheaper staff, which may represent a cost saving, but you now have internet problems added to the load of the more experienced staff who now have a ‘richer mixture’ to contend with.
Look again at the example of the changes to your paper process after introducing an internet option.
So although the internet option in my example means a small overall saving of 4% in staff time, it has also altered the balance of staff. Previously, I needed 35% experienced staff in my data capture department. Now I need 62%. Let’s hope that I didn’t move my experienced staff to the internet forms helpline.
Investigate your costs
I have spent a lot of time explaining what might go wrong and how those problems might end up giving you trouble on your own project. Against that, there are many success stories and the opportunity to remove tedious work. So how can you find out what the risk factors are on your own project?
You need to find out the mix of forms and the time to deal with them
My calculations used:
- categorisation of forms into 5 types: ‘easy’, ‘ordinary’, ‘internal fix’, ‘go back’ and ‘rework’
- percentage of each type in the overall workload
- post handling time
- keying time
- recognition rate for properly completed boxes
- percentage of validation failures
- scanning time
- percentage of recognition failures because of improperly completed boxes (‘extra marks’ and other errors)
- penalty percentage on dealing with problems in a different order because of automated process
- increase in rework category
and I also warned you about capturing data you already know, data that arrives twice, or data which you may not use.
I use four investigating techniques
The four techniques are:
1. Cohort tracking
2. Exceptions analysis
3. Usage analysis
4. System calibration
1. Cohort tracking helps you to find out about the overall elapsed time to process
Cohort tracking will define:
- your own types for categorisation of forms
- your own percentage of each type in the overall workload
- the post handling time.
The steps are:
1. Make an appointment with your post room. Find out when they open the post, and what the pattern of post is from day to day and week to week. Choose a typical day for your first cohort.
2. Count the unopened envelopes. You may need to start selecting at this point. If you have thousands of items, it will be hard to track them all, so you may need to compromise by picking every tenth, or every hundredth envelope.
3. Watch your envelopes being opened. Note how many items are removed for separate handling. Note how many of the items arrive with or without supporting information. Establish how much work gets done on your items.
4. Mark each item you are interested in. You could use a small rubber stamp, or a dot of highlight pen, on the reverse of the item.
5. Take note of some identifying number for each item. This could be the customer number or some other identification.
6. You now have a cohort of items.
The idea is to check back to see how many have been dealt with and what happened to them. Who sorts them, and why? How many are
finished with by the end of day 1, of week 1, of month 1? Did any of them turn into complaints?
By tracking your cohort through the process, you should be able to create your own split of your documents into the ‘easy’, ‘ordinary’, ‘internal fix’, ‘go back’ and ‘rework’ – or a more complex selection of categories.
Depending on the overall time for your process, you may need to check on your cohort over days, weeks or even months. If you do not do it, you may miss the really time-consuming examples that eliminate any savings from an automated process.
If the typical cohort shows encouraging figures – low percentages in the ‘go back’ and ‘rework’ categories – then you may need to track more cohorts, choosing them from the extreme or unusual: end of the month, the day after bank holiday, extra orders after a big promotion.
Exception analysis helps you to find your repair and error rates
Cohort tracking identifies the overall fate of a batch of items. Exceptions analysis is its opposite: it looks at the work of a single day, or even of a single hour, and identifies the full range of problems encountered during that particular session of processing.
Exceptions analysis will define:
- keying time
- percentage of validation failures
- percentage of recognition failures because of improperly completed boxes (‘extra marks’ and other errors).
This time, you start with the forms as they arrive at the point of capture. You may need to enlist the help of the staff who deal with the form. For each form and every field on the form, you note:
- if you find the writing on the form difficult to read
- whether there are extra marks
- if any field is completed in a way which might fail validation
- if anything mandatory is missing
- if there are internal contradictions, for example two items both completed, when only one is allowed
- if there are any marginal notes, additional information, or accompanying letters to explain entries on the form.
By the end of this, you should be able to identify:
- the percentage of forms with extra marks
- the rate of validation errors
- the rate of internal fix errors
- the rate of ‘go back’ errors
Of course, you could do the exceptions analysis on the cohort. But often the cohort gets split up during its various sorting phases – and you find that you can only look at exceptions with particular members of staff who do certain types of work. The cohort tracking gives you the overall mixture, whereas the exceptions analysis gives you the detail on elements of the mixture.
Usage analysis helps you to find out how you use the information you ask for
The third step is usage analysis. This tells you how you use the information you ask for on the form.
Do not try this step until you have your cohort and exceptions information. If you use a blank form, you will find that there are unrealistic expectations about the standard of accuracy in the information written on the form.
Armed with the data about what actually gets put onto the form by your customers, you convene a meeting – or it may have to be a series of meetings – of your computer team, your processing team, and the overall owner of the business process. For every box on the form, you find out:
- what gets put into the computer system by the processing staff
- what the computer system does with that information
- the consequences for the business of the exceptions you have identified.
The meeting should discover the discrepancies between what you ask for and what you need.
System calibration helps you to create a benchmark for your process
By the end of the cohort tracking, exceptions analysis and usage analysis, you should be able to judge whether your data process is sufficiently straightforward to allow you to consider an automated process. My broad criteria would be:
- 20% or fewer forms have exceptions
- you are using all the information you ask for, and
- more than 90% of forms fall into the ‘easy’ or ‘ordinary’ categories.
You can now prepare a realistic pack of test forms to discuss with your chosen vendors. The pack should include the same mixture of types of documents as your overall mix, discovered during the cohort tracking.
Remember to put them into the appropriate envelopes: the folding is important. During system calibration, you will discover:
- effect on post handling time
- scanning time
- recognition rate for properly completed boxes
- percentage of recognition failures because of improperly completed boxes (‘extra marks’ and other errors)
- penalty percentage on dealing with problems in a different order because of automated process
- increase in rework category.
Test the proposed scanner by getting the forms out of their envelopes, sorting them as required by your vendor, and scanning them. Ask your vendor to provide you with the recognition rates and recognition failures on your test pack of forms. Do not accept rates produced on any other test pack. Finally, check the output data you are likely to obtain. Will this be sufficiently accurate to prevent any increase in rework?
The bottom line is that people make mistakes
Every data capture application has to accept that people will make mistakes. Your new automated system will just expose the problems that your current manual system avoids by using the perceptual and judgmental skills of your staff. Your new internet system forces your customers to solve problems that your staff deal with at the moment.
Often, these skills come as a surprise. Your post-room staff and data entry clerks are often some of the lowest-paid employees in the business. Despite this, they are making hundreds of decisions every day. They may be relatively tiny decisions, but the cumulative effect can be fundamental to your business.
If you want to save costs by implementing new technology, you must:
- find out how your forms are filled in
- find out what your staff actually do
- understand what your business does with the forms and data.
What you learn should help you to win, not lose, from implementing your new technology. Or you might decide to improve some of the old technology. How about some hand-cream for the staff who open the post?